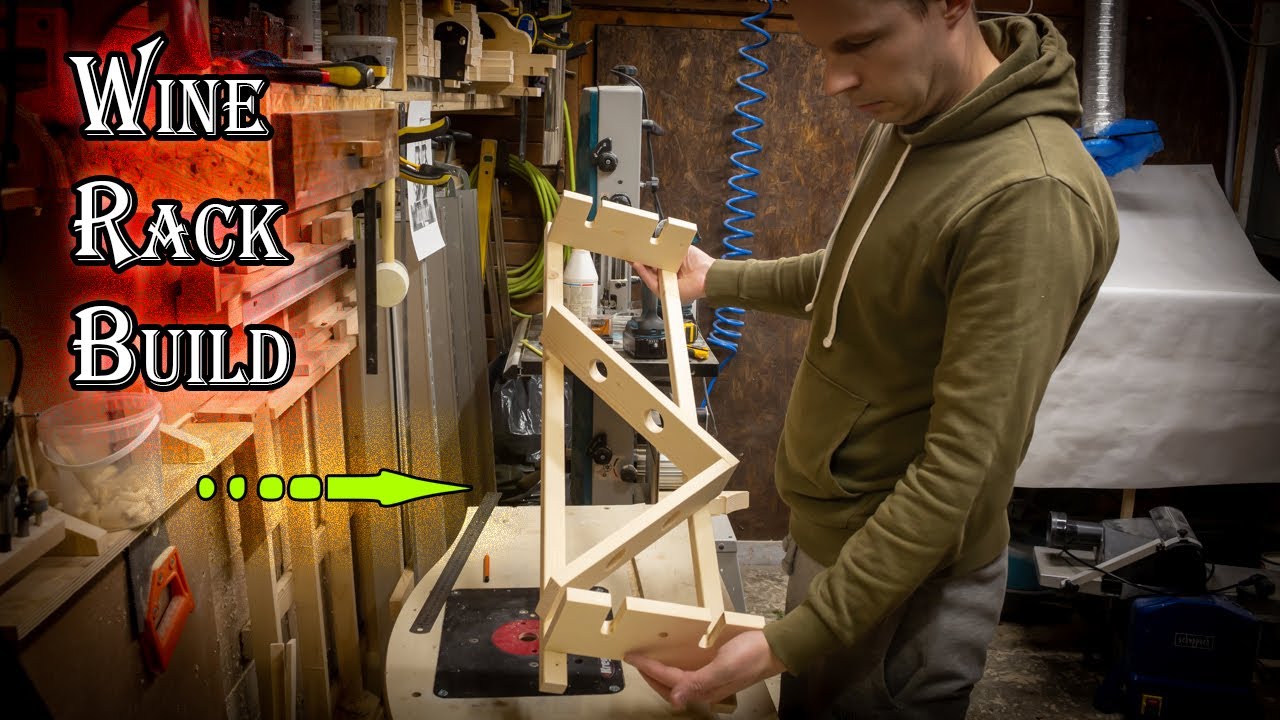
Building a Wine Rack from Reclaimed Wood: A Guide to Rustic Elegance
Reclaimed wood, with its unique character and history, offers an exceptional material for crafting a wine rack that adds a touch of rustic charm to any space. Its natural beauty and sustainability make it a popular choice for discerning homeowners. This comprehensive guide will walk you through the process of building a stunning wine rack from reclaimed wood, ensuring a functional and aesthetically pleasing piece that showcases the raw elegance of this versatile material.
Choosing the Right Reclaimed Wood
The first step in building a wine rack from reclaimed wood is selecting the right material. Consider the following factors:
Wood Type:
Reclaimed wood can come from a variety of sources, including old barns, houses, and even pallets. Choose wood species that are known for their durability, such as oak, pine, or cedar. The grain pattern and color of the wood will also influence the overall aesthetic of the rack.
Condition:
The condition of the reclaimed wood will affect its usability. Inspect the wood for signs of rot, infestation, or significant warping. While some imperfections can add character, excessive damage may make the wood unsuitable for construction.
Thickness and Width:
The thickness and width of the reclaimed wood boards will determine the structural integrity and design possibilities of the wine rack. Thicker boards provide greater stability, while wider boards can accommodate larger bottles.
Planning the Design
Once you have chosen the reclaimed wood, it's time to plan the design of your wine rack. Consider the following factors:
Size and Capacity:
Determine the desired size of the rack based on the space available and your wine collection. Consider the number of bottles you need to store and the width of the shelves to accommodate different bottle sizes.
Shape and Style:
The shape and style of the wine rack can be customized to complement your décor. Popular options include freestanding racks, wall-mounted racks, and even wine racks with integrated bottle holders. Choose a design that aligns with your personal preferences and the overall aesthetic of your space.
Features:
Consider additional features that enhance functionality and aesthetics, such as built-in bottle stoppers, glass holders, or decorative elements like metal accents or vintage hardware.
Preparing the Reclaimed Wood
Before starting construction, properly prepare the reclaimed wood to ensure a smooth and durable finished product:
Cleaning and Drying:
Thoroughly clean the reclaimed wood to remove dirt, debris, and any remaining coatings. Allow the wood to dry completely, either naturally or with a dehumidifier, to prevent warping during construction.
Cutting and Shaping:
Cut the reclaimed wood boards to the desired dimensions using a circular saw, miter saw, or table saw. Use a jigsaw or hand-held saw for intricate cuts and shaping. Ensure all cuts are precise to ensure proper alignment and stability.
Sanding:
Sand the reclaimed wood boards thoroughly to remove any rough edges or imperfections. Start with a coarser grit sandpaper and gradually progress to finer grits to achieve a smooth finish. This step will also help create a uniform surface for staining or painting.
Construction Steps
Follow these step-by-step instructions to build your reclaimed wood wine rack:
Assembling the Base:
Create a sturdy base for the wine rack using two or three long pieces of reclaimed wood joined together with wood glue and screws. Ensure the base is level and secure to prevent wobbling.
Building the Shelves:
Construct each shelf using two or more pieces of reclaimed wood, depending on the desired width. Join the pieces together using wood glue and screws. Ensure the shelves are cut to the exact length and width to fit properly on the base.
Attaching the Shelves to the Base:
Attach the shelves to the base using wood glue and screws. Position the shelves evenly and secure them firmly to prevent sagging. Add decorative elements or braces for added support if desired.
Finishing Touches:
Once the wine rack is assembled, apply a protective finish to enhance the beauty and longevity of the reclaimed wood. Consider options such as:
Safety Precautions
When working with reclaimed wood and power tools, it's essential to prioritize safety:
Conclusion
Building a wine rack from reclaimed wood is a rewarding project that allows you to create a unique and functional piece that showcases the beauty of this sustainable material. By following these guidelines, you can craft a rustic and elegant wine rack that adds charm and character to your home while responsibly repurposing old wood.